An Invested Leader in ATE
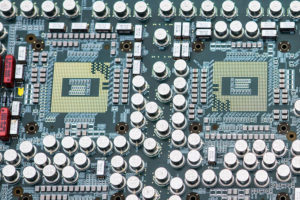
ATE/Load Board Assembly
SEM has been building load boards for the leading companies in the industry for over 10 years and has been a reliable contract manufacturer in Silicon Valley for more than 24 years. We have invested a tremendous amount of time, effort, and finances into our facility, equipment, and training so that we can offer the newest technology and most advanced services for the ATE industry.
Load boards used in the semiconductor chip testing process on Automated Test Equipment (ATE) are large, heavy, and thick boards; an average of over 40 layers with complex packages and high component counts. The design of load boards is a complex process in which the scope of the design is comprehensive but with many process limitations. Design engineers often compromise DFA rules for both PCB fabrication and assembly to achieve their desired design requirements which may cause an unavoidable delay in the assembly process and overall schedule.

ATE/Load Board Assembly
For this reason, DFA analysis before the fabrication and assembly process is critical. SEM has top-of-the-line DFA tools, which we use to review and validate multiple projects every day. We work with the design engineers to resolve problems before the project is released to fabrication to help save on the cost and schedule while enhancing the efficiency and reliability of the final product. We use a single source tool to create all programs used for the equipment and processing of the boards, which streamlines all areas of production.
SEM works with its customers to define, optimize, and validate complicated processes for specific build requirements. Our team processes hundreds of load boards per month on 1, 2, and 3-day turns while maintaining superb quality and reliability of all products. SEM has a dedicated team, loaded with experience and ready to translate it to successful products for our customers.